O coalescedor AquaSep® da Pall remove água de diesel, após unidade de hidrotratamento em uma refinaria
Desafios
Uma grande empresa canadense de petróleo opera uma refinaria de 138.000 bbl/dia perto de Edmonton, na província de Alberta. A refinaria produz diesel com teor ultrabaixo de enxofre (ULSD), usando vapor leve ou pesado no processo. As vazões de vapor são proporcionais a 21.875 bbl/dia e 36.590 bbl/dia de diesel. O hidrotratamento é uma tecnologia licenciada pela UOP. Ele emprega extração de vapor para fracionar o produto hidrotratado.
A extração de vapor é uma opção mais econômica para o fracionamento (em comparação a reboilers). Entretanto, ela cria uma emulsão estável, devido à formação de gotas extremamente finas quando o vapor se condensa em destilado. A emulsão estável resultante é difícil de quebrar com dispositivos Knock-Out ou tecnologias de coalescedor líquido/líquido tradicionais.
As separações da emulsão estável não são bem entendidas pelo setor de refino, licenciadores de processo e empresas de engenharia.
A empresa de engenharia adquiriu um coalescedor líquido/líquido horizonal com mesh pad de um grande fabricante de separadores para o projeto ULSD. Esse coalescedor não foi capaz de quebrar a emulsão, levando a uma vida útil do secador muito curta. As amostras da entrada e da saída ao redor do coalescedor mesh pad tinham a mesma aparência.
A unidade ULSD da refinaria sofreu uma paralisação inesperada, pois estava operando sem capacidade de armazenamento para o destilado contaminado que exigia reprocessamento. (Foram necessários diversos dias de decantação para reduzir as concentrações de água livre de 600 ppm para 250 a 300 ppm, indicando que uma emulsão muito estável foi produzida.)
Uma solução de curto prazo para se manter em operação, o leito de sal foi substituído por uma peneira molecular que possui recursos de adsorção de água mais altos do que o sal. A refinaria não tinha recursos para regenerar o meio da peneira molecular, então ela foi substituída quando gasta. Essa foi uma medida emergencial muito cara.
Após falhas em remediar os coalescedores de mesh pad no verão de 2006, a Pall Corporation foi convidada a demonstrar sua tecnologia de coalescedor AquaSep® no cliente.
O teste no local foi realizado para estabelecer parâmetros de dimensionamento e a eficiência da separação da água. A concentração de água total na unidade de teste nos dois fluxos foi de aproximadamente 600 ppmv, com temperaturas operacionais de 30 a 33 ˚C (86 a 91 ˚F). Após a unidade de teste piloto, a concentração de água livre no diesel leve variou entre 5 e 12 ppmv. No destilado pesado, a variação foi de 3,5 a 10,5 ppmv de água livre, medida pelo método Gammon Aqua-Glo1. A empresa de petróleo canadense precisava produzir diesel de acordo com as especificações e precisava disso imediatamente.
Solução
A Pall, líder do setor em tecnologia de produtos químicos e polímeros estava mais do que pronta para assumir o desafio. Os técnicos da Pall avaliaram os desafios da refinaria e decidiram que o coalescedor AquaSep® seria a melhor opção para a tarefa. O coalescedor de diesel AquaSep da Pall separaria de modo eficiente a água do vapor de hidrocarboneto sem desarmar o coalescedor. Além disso, o custo total da separação do líquido é baixo… especialmente quando comparado a outros métodos menos eficientes.
Depois de um teste bem-sucedido no local e envio da proposta, a refinaria fez um pedido de pré-filtros verticais e dos coalescedores AquaSep L/L para os dois fluxos. O pedido foi feito em agosto de 2006, com entrega rápida do equipamento exigido até 31 de outubro, antes da chegada do inverno. (Durante os meses de inverno, o destilado pesado é iso-desparafinado para reduzir o ponto de nuvem. A unidade IDW exige um fluxo de alimentação sem água.) O seguinte equipamento foi despachado:
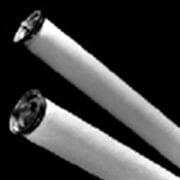
Sistema de coalescedor AquaSep Plus
A separação eficiente de líquido e os recursos de remoção de particulado do sistema de coalescedor de diesel AquaSep Plus reduzem significativamente os incidentes com produto fora da especificação, economizando assim custos de reprocessamento e transporte.
Diesel leve:
Pré-filtro: 7HFH62408F3-280-CS com elementos HFU660GF020H
Coalescedor: 37AQH3608F3-280-CS com coalescedor/elementos do separador LCS4B1AH e LSS2F1H
Diesel pesado:
Pré-filtro: Duplex 12HFH63008F3-280-CS com elementos HFU660GF020H
Coalescedor: 59AQH4808F3-280-CS com coalescedor/elementos do separador LCS4B1AH e LSS2F1H
O pré-filtro de destilado pesado e os filtros coalescedores de diesel entraram em operação em 20 de dezembro de 2006. Os níveis de água totais a jusante eram de 140 ppm (pelo método de filtração Karl Fischer) e o efluente era “claro e brilhante” (dentro dos objetivos exigidos). O reservatório do coalescedor era drenado a cada 30 minutos. A refinaria estava operando a stripper de forma mais agressiva do que o previsto. A extração extrema maximizou a produção de destilado leve devido às demandas do mercado.
Isso aumentou a viscosidade além das especificações do projeto de 6,1 cps a 8,5 cps no destilado pesado. O coalescedor continuou a operar conforme projetado, mesmo com viscosidade maior.
Resultados
A refinaria ficou feliz com o desempenho da instalação do coalescedor de filtro de diesel. Eles disseram que “o coalescedor da Pall funcionou conforme o prometido.” A incapacidade de produzir diesel de acordo com as especificações era vista como o maior problema enfrentado por essa empresa de petróleo no momento.
No futuro, a refinaria pretende operar com peneira molecular na linha para remover água dissolvida do ULSD. As peneiras moleculares serão regeneradas com o destilado quente e pesado diretamente do fracionador. O destilado com água será então reciclado de volta para o coalescedor AquaSep para separação da água livre. A maior vida útil do coalescedor e a eficiência superior de separação de líquidos são definidas para ajudar a minimizar o tempo de inatividade e ajudar a refinaria a economizar nos próximos anos.
Vamos encontrar a solução certa juntos.
Vamos nos conectar. Queremos compartilhar nossas soluções de filtração inovadoras com você hoje mesmo. Entre em contato com nossos especialistas no assunto para informações sobre como podemos ajudar. Obrigado e esperamos apoiar você em breve.