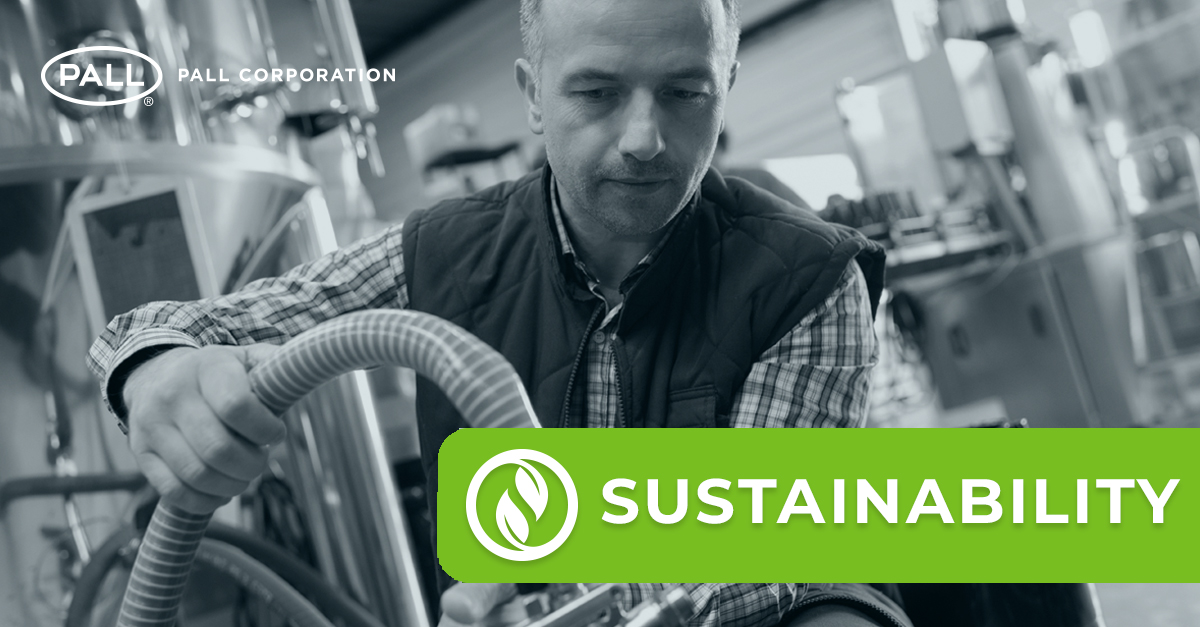
Using Filtration Technologies to Improve Sustainability Initiatives
April 20, 2021
If your food or beverage brand hasn’t considered ways to become more sustainable, it should start. Sustainability initiatives not only help save the environment, but also drive consumer purchasing decisions. According to a 2020 Euromonitor Lifestyles Survey, more than a quarter over those surveyed said they boycott brands that do not align with their ethical values. This means communicating sustainability strategies is starting to play an increasingly important role in a business’ success.
A 2019 article in Harvard Business Review states that products that had a sustainability claim on-pack accounted for 16.6% of the market in 2018, up from 14.3% in 2013, and delivered nearly $114 billion in sales, up 29% from 2013. The biggest takeaway from the study: “products marketed as sustainable grew 5.6 times faster than those that were not.”
So how can you make your brand more appealing to consumers?
One way to start is to look at your current manufacturing processes to identify areas of improvement. In your site’s current state, can you confidently claim that the technologies you use minimize waste, optimize energy efficiency and reduce water consumption?
Even if you are already employing sustainable methods in your processes, filtration technologies can still bring further improvements. For example, did you know that filtration technologies can improve your overall process efficiency and reduce your OPEX, thus supporting more sustainable manufacturing practices? It’s worth investigating the options available, such as using membrane-based filtration systems to achieve optimal results.
Using Filtration Systems to Reduce Waste
For many manufacturers, the Diatomaceous Earth (DE) filters are one of the most common filtration methods even though they can be inconsistent, challenging to use and maintain, and the handling and disposal of DE filters requires special handling to avoid operational health risks.
DE disposal expenses can easily exceed the cost for fresh DE by factor 1.5 to 3. Take for instance a brewery producing one million Hectoliters (HL) per year. By leveraging membrane-based beer clarification systems, the brewery can eliminate a significant amount of spent DE. That’s quite an impressive feat and one that consumers would be interested in knowing more about.
Leveraging a DE-free alternative such as a membrane filtration system eliminates these costs as well as the aforementioned issues associated with the use of DE filters. Moving away from DE to membrane filtration allows you to leverage a beer system that does not generate high-levels of waste, but instead produces higher clarity and better product quality every time, in a safe and easy way.
Using Filtration Systems to Reduce Energy and Water Consumption
Another way to become more sustainable is through reducing energy consumption. Many beer manufacturers use tunnel or flash pasteurization but leveraging cold membrane filtration in your beer production process can result in a significant reduction in energy consumption and OPEX in addition to other operational benefits.
The main advantage of cold filtration is the direct installation of the filter upstream of the filling line without a buffer tank. Membranes with a stable matrix maintain their separation characteristics at varying flow rates and pressures including start/stop situations. This provides maximum microbial safety, combined with minimum beer losses and true flexibility in terms of brand changes and start/stop operation.
Eliminating the buffer tank upstream of the filling equipment avoids a critical recontamination point, minimizing beer losses at production start and at brand changes and reduces expensive CO2 consumption.
A filtration system that hosts an individual cluster housing design also means that consumption of water, cleaner and enzyme is reduced by 25 to 30% compared to the big vessel cluster systems and up to 45% compared to standard multi- round housing design concepts. The low hold-up volume and higher throughputs of membrane filter systems result in less water and energy needed for rinsing and cleaning.
The water and energy savings of membrane filtration compared to thermal treatment installations is significant. Flash pasteurizers waste up to 75% more water and consume up to 80% more energy on the thermal and electric side. Water and energy consumption of tunnel pasteurizers is even higher.
Conclusion: Process Changes Yield Sustainable Results
If you’re trying to implement sustainability initiatives in your food and beverage manufacturing process, consider starting with filtration. Leveraging filtration systems to support your initiatives can lead to quantifiable waste and energy usage reduction claims which will catch the eye of your consumer when shared on your website, advertising and product packaging.
In addition, it’s always nice to partner with filtration manufacturers who practice what they preach. Leveraging supply chain partners who also implement sustainability initiatives is a winning combination to further improve the quality of Mother Earth, while meeting consumer demand for better business practices.
Aligning with consumer values such as environmental and ethical business practices will benefit your brand and implementing filtration technologies can achieve surprising results, promoting environmental stewardship and impacting your bottom line.
- Category
- Author
- Sort By