The Chain Reaction of Wear
In a study by the late Dr. E. Rabinowicz of M.I.T., the observation was made that 70% of component replacements or "loss of usefulness" is due to surface degradation. In hydraulic and lubricating systems, 20% of these replacements result from corrosion, with 50% resulting from mechanical wear.
Particles generated as a result of abrasive wear are work hardened; thus they become harder than the parent surface. If these particles are not removed by proper filtration, they will recirculate and cause additional wear. This "chain reaction of wear" will continue and result in premature system component failure unless high-performance filtration is applied to break the chain. That answers the question, ‘why is filtration important?’.
Supralon ® filters with ß x= 2000 removal efficiency ensure cleaner fluids for long component life, maximum system reliability, and lower operating costs.
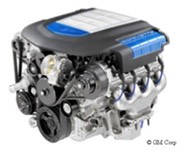
Abrasive Wear
These are the different wear types to look out for.
Particles generated as a result of abrasive wear are "work hardened;" they become harder than the parent surface and, if not removed by proper filtration, will recirculate to cause additional wear. Here's how it happens:
Particles enter the clearance space between a component's two moving surfaces, bury themselves in one of the surfaces, and act like cutting tools to remove material from the opposing surface. The particle sizes causing the most damage are those equal to and slightly larger than the clearance space. Ultimately, abrasive wear will result in dimensional changes, leakage and lower efficiency. Left uncontrolled, more particles will be generated which will result in a chain reaction of abrasive wear -- a chain reaction that will continue and cause premature system component failure unless adequate filtration is implemented to break the chain. To protect components from abrasive wear, particles of approximately the dynamic clearance size range must be removed.
Erosive Wear
Erosive wear is caused by particles that impinge on a component surface or edge and remove material from that surface due to momentum effects. This type of wear is especially noticed in components with high velocity flows, such as servo and proportional valves. Particles repeatedly striking the surface may also cause denting and eventual fatigue on the surface. The damaging effects of wear types such as erosive wear can be seen in dimensional changes to equipment, leakage, lower efficiency, and the generation of additional particles, which leads to further contamination and wear throughout the system.
Fatigue Wear
Bearing surfaces are subjected to fatigue failures as a result of repeated stress caused by particles trapped between the two moving surfaces. At first, the surfaces are dented and then cracking begins. These cracks spread after repeated stress by the bearing load, even without additional particulate damage, and eventually the surface fails, producing a spall. When wear types like this occur, contamination reduces bearing life significantly through fatigue, abrasion and roughening or degradation of operating surfaces.
Water and Air Contamination in Oil
Water and Particulate Removal Using the Pall HSP Purifier
Water contamination in oil can cause a fluid breakdown, reduce lubricating film thickness, accelerate metal surface fatigue, corrode components, and lead to a loss of dielectric strength in insulating fluids. The main sources of water contamination are heat exchanger leaks, seal leaks, condensation of humid air, inadequate reservoir covers, and temperature drops which lead to dissolved water (below saturation) becoming free water (emulsified or in droplets). Both free and dissolved water cause component and oil degradation. When conducting fluid sampling, if oil becomes milky in appearance, the saturation limit at the oil temperature has been exceeded, indicating that both dissolved and free water are present.
Air and Other Gas Contamination
Dissolved air and other gases in oils can cause foaming, slow system response with erratic action, a reduction in system stiffness, higher fluid temperatures, pump damage due to cavitation, an inability to develop full system pressure, and an acceleration of oxidation.
Why Is Filtration Important? - Measuring Filter Performance
The Multi-Pass Performance Test
The multi-pass filter performance test is internationally recognized as the most reliable means to obtain consistent and repeatable information on a filter's ability to control specific-sized particles.
The multi-pass 'beta' (ß) test challenges the filter in a similar manner as an operating system would!
Here's how
- Fresh contaminant is introduced in a slurry form into the test reservoir, mixed with the fluid in the reservoir, and pumped through the test filter.
- Contaminant not captured by the filter is returned to the reservoir for another pass through the filter (thus the name "multi-pass")
- Upstream and downstream fluid samples are analyzed to determine their respective particle counts.
For more informationon wear types and how our technology deals with them, read about our test stands for automotive, industrial components.
Our Products
Leading the Industry with product solutions that fit your customers needs.
How can we help?
If you are looking for innovative filtration solutions, you’ve come to the right place. Our knowledgeable subject matter experts are here for you. Contact us for more information. Thank you and we look forward to assisting you shortly.