Unmatched Value and Reliability
Long-lasting, cost-effective, protection to ensure peak performance.
Our premium filtration and separation technologies for the primary metals industry deliver durable filtration performance with high-capacity filters for longer service life to enhance product quality and reduce the frequency of both scheduled and unscheduled maintenance activities. With our primary metal filtration technologies, end product quality is enhanced while operating costs are dramatically reduced for a direct and positive impact on business performance.
Primary metals processes can be sensitive to the presence of contaminants. Intense global competition has caused producers of steel, aluminum and other metals to do everything they can to lower production costs and adopt new, more efficient technologies. we have a long history of working with these primary metals industry leaders to provide cost saving solutions and process improvement. We offer a wide range of long-lasting, cost-effective, industrial filter products. Our fluid conditioning equipment and condition monitoring devices work to safeguard industrial equipment reliability and ensure peak performance.
For more information on improving the efficiency of your processes, contact our team of filtration experts.

We offer a wide range of long-lasting, cost-effective, filter products.
Primary Metals Applications
» View All Primary Metals ProductsPRIMARY METALS Products
For more information about our range of products, explore our product catalog.
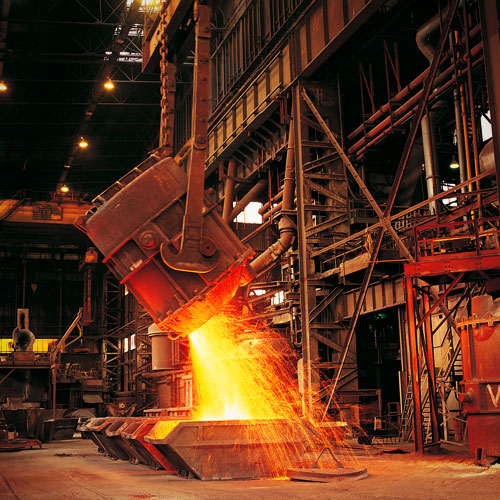
Coolants and bearing lubrication
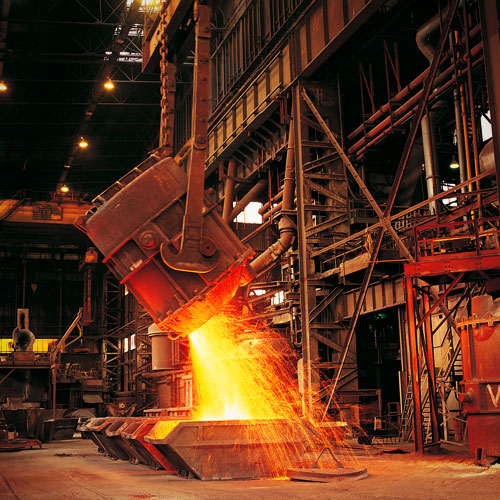
Drives gear box and roll housing
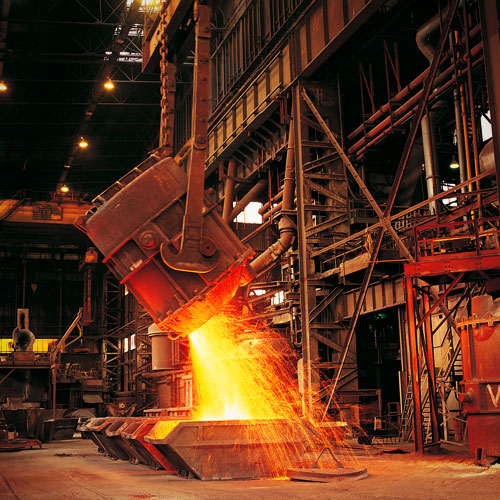
Forging and extrusion
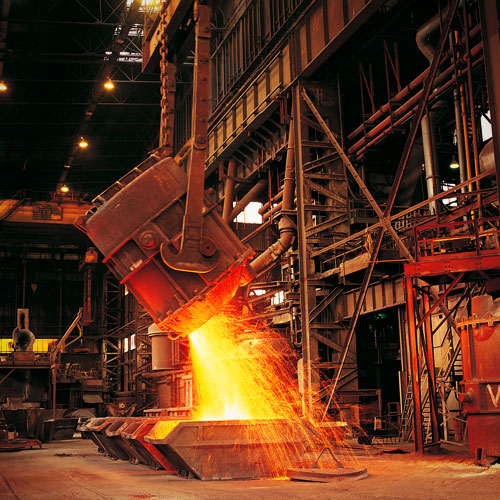
Gear Box and bearing
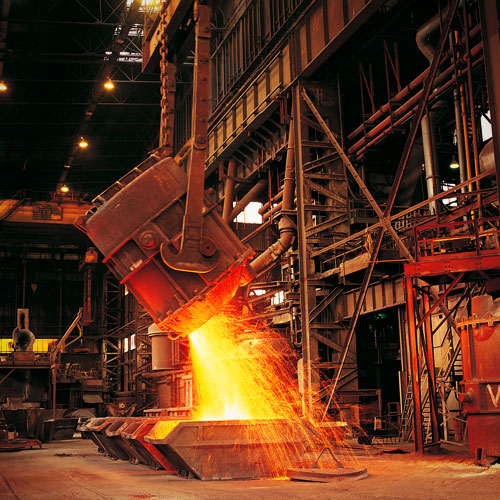
Gear box and morgoil
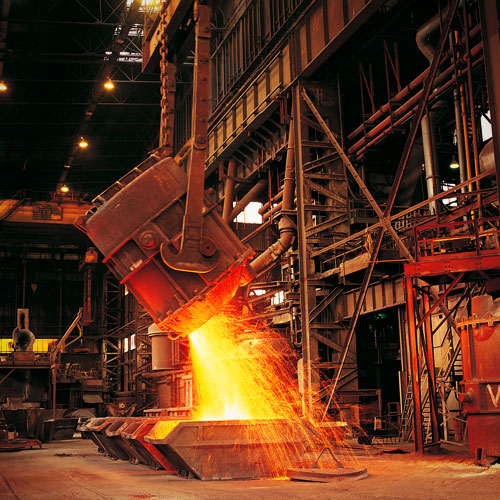
Material directional control
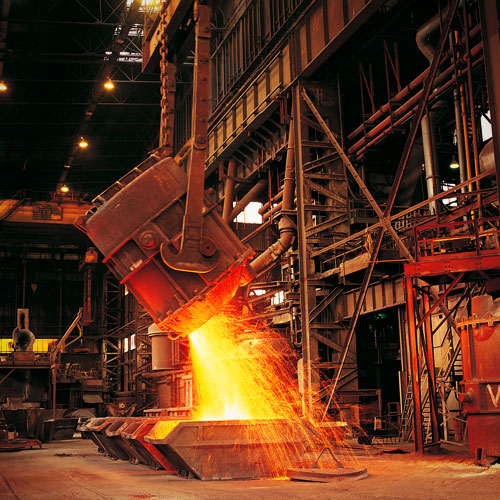
Material handling
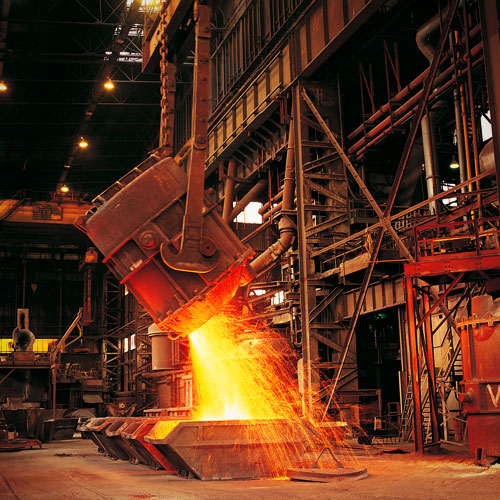
Roll bite (safety filter)
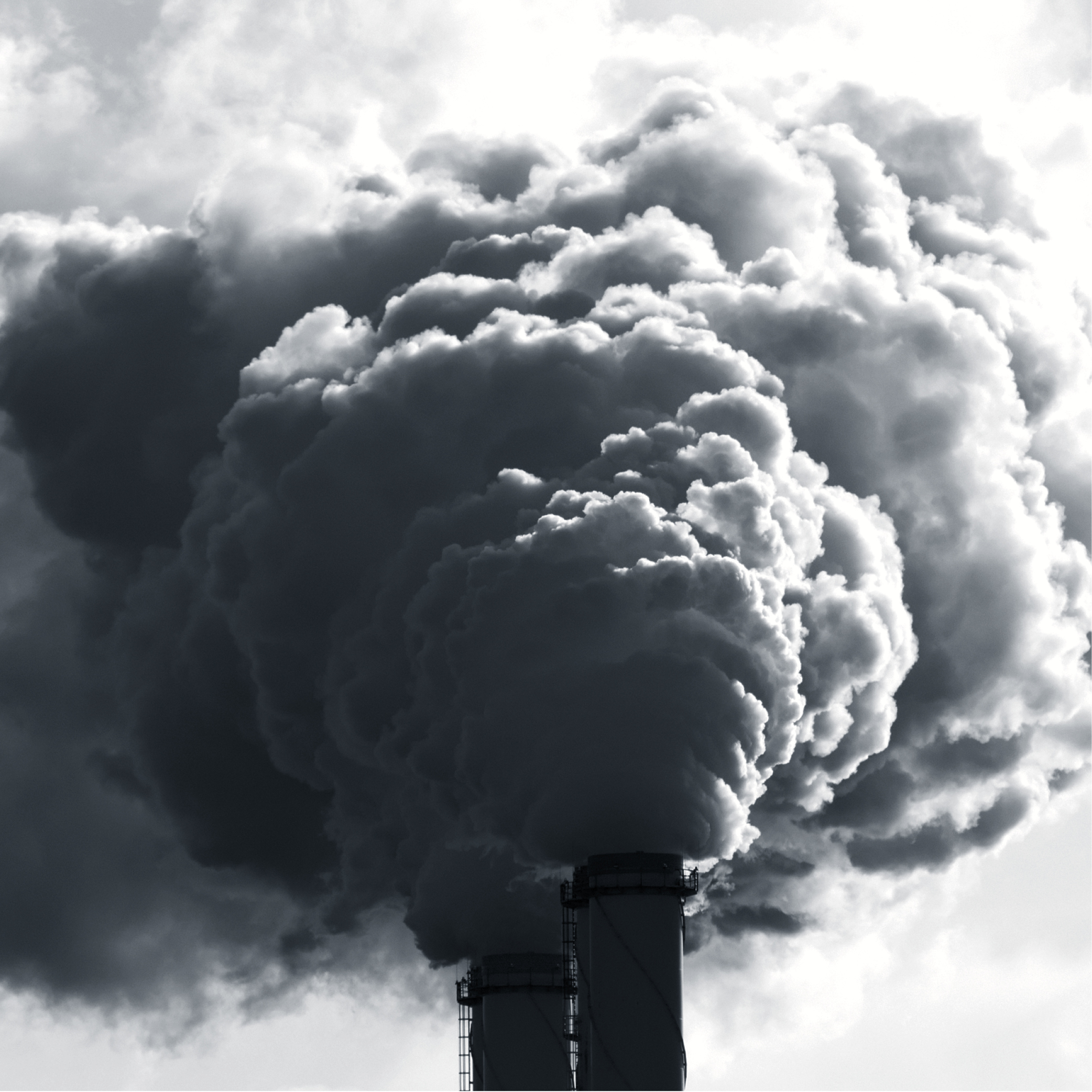
Carbon Capture and Storage
Primary Metals Solutions
Enhanced reliability, resulting in efficient and optimized industrial operations and superior end products.
Wherever fine filtration and optimum cleanliness is required, We offer a tailored product for the primary metals industry. Our contamination control solutions are applied to servo-hydraulic systems such as electric arc furnaces, roll positioning, continuous casters and automatic gauge controls. They are also used in lubrication systems including rod mills, rolling mills, foil mills, extrusion operations and forging operations.
Keeping large particulates out of metal manufacturing operations equipment is vital to the metal manufacturing industry. Our filtration and purification products reliably and economically reduce the level of large particulates in hydraulic or lubrication systems and ensure optimum fluid cleanliness levels, consistent performance and long service life for the lowest cost of operation.
Predictive maintenance programs including oil analysis and condition monitoring have become commonplace throughout the industry. Our filtration and purification products reliably and economically reduce the level of particulate and water contaminants in hydraulic or lube systems. Our filter elements, purifiers and housings ensure optimum fluid cleanliness levels, consistent performance and long service life for the lowest cost of operation.
Contact our team of primary metal filtration experts to learn more about our advanced filtration solutions for primary metal manufacturing today!
Check out our Athalon case study on how one customer upgraded to Athalon hydraulic return line filter elements for easier servicing and improved system protection!
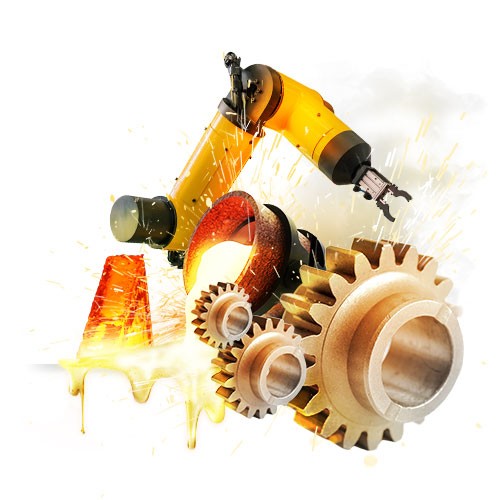
Our filtration and purification products reliably and economically reduce the level of particulate and water contaminants in hydraulic or lube systems.