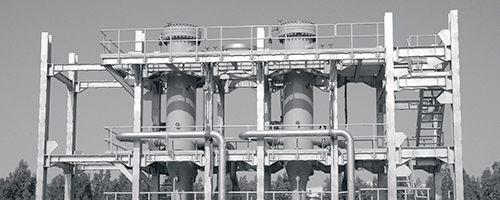
Blog
The Impact of Black Powder on Furnace Feeds and How to Remove it
What is black powder?
Black Powder is a common corrosion-related contaminant prevalent in pipelines transporting LPG, LNG, and hydrocarbon condensates. Studies of particle size distribution have shown a variation in size from fine to sub-micronic. It’s referred to as being black generally due to visual appearance, which is often black or grey, but it can equally be a lighter color. The typical composition of black powder is iron oxide, accelerated by sour gas and poses a significant threat to pipeline integrity.
The Impact of Black Powder
The presence of black powder in incoming LNG/LPG to ethylene furnaces can negatively impact their performance. As a result, furnace run times decrease while maintenance costs are higher.
Other consequences include:
- Accelerated coking reactions in the tubes and fouling in the convection section
- Formation of CO in cracked gas
- Loss of furnace capacity during pigging operations of the pipelines
- Severe corrosion resulting in frequent replacement of damaged furnace tubes
In natural gas pipelines, the problems caused by black powder and water/hydrocarbon include:
- Product with high water content in condensate or crude that upsets the process
- Foaming in amine sweetening units and glycol dehydration units
- Equipment failures leading to fouling and plugging of reboilers in the fractionation plants
- Poor accuracy of meters/valves
- Failure of critical instrumentation
- Safety and environmental issues such as gas releases
Sample Collection
Black Powder can vary considerably in size distribution, quantity, and chemical composition. A site survey is crucial before implementing separation technology to assess pipeline contamination issues. This way, the site-specific contaminant characteristics can be determined and used as a guideline for selecting the optimized separation system.
Isokinetic sampling is recommended as the best practice to avoid altering particle size. This technique collects particles in a stream moving at the same velocity in the sampling nozzle as elsewhere in the stream, which increases the accuracy and reliability of results. Other methods measure the liquid content and size distribution of liquid aerosols, including in-line particle counters. However, these cannot distinguish liquid aerosols from solid particulates, and they cannot collect liquids.
Filtration/Separation Techniques Used
There are a variety of commercial solutions available to the natural gas industry to mitigate the impact of black powder by removing water/hydrocarbons from gas. These include:
Several different filter materials are available. Cellulose, glass fiber, and polypropylene are the most common types. Filters must be absolute rated for maximum performance. Find our more about filter ratings in our filtration fundamentals blog here.
For natural gas pipelines with significant amounts of suspended solids, cartridge filters and Cyclone Separators are appropriate. Particles larger than 5-10 microns are removed from the cyclone system via the cartridges downstream of the cyclone product. The cyclone generates a low-pressure drop since it operates at a lower velocity flow. This combination is capable of handling high solid loadings, including contaminant slugs.
Water/hydrocarbon removal in the incoming gas is best achieved via a high-efficiency liquid-gas coalescer if the contaminant is present as aerosol droplets. Separation occurs through a range of mechanisms depending on the size of the droplet. These include knock-out drums, demister pads, vane packs, and liquid/gas coalescers.
Similarly, liquid/liquid separators remove discontinuous liquid phases from another liquid. Typical applications include removing brine or hydrocarbons in liquefied natural gas feedstocks that enter ethylene cracking furnaces. Before the liquid/liquid coalescer, a prefilter eliminates black powder solid contamination down to 10 microns. The prefilter will protect and prolong the life of the coalescer, which breaks the emulsion of the contaminants in the liquefied gas.
To find out more about our range of solutions to suit your needs, visit our dedicated midstream black powder removal page .
- Category
- Author
- Sort By