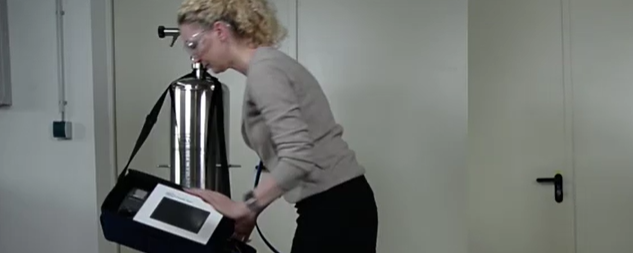
Blog
Final Membrane Filtration and Integrity Testing: The Insurance Policy You Never Knew Your Brand Needed
February 24, 2021
To safeguard your product and ensure its consistency, final membrane filtration is an established and can be a crucial step in your process. By acting as a physical barrier, final membrane filtration provides product stability and more specifically removes cells, or cell debris that can potentially enters your food or beverage product. Specific membrane filters can also provide sterile effluent at point of use.
The consequences of spoilage microorganisms include:
- Product recalls which endanger both your customer and your brand,
- A tarnished brand reputation that significantly impacts consumer trust in your products,
- And lack of product consistency that can affect the taste, flavor and aroma.
Maybe at first glance those consequences don’t seem scary, but product recalls can cost your business millions of dollars in regulatory fines. And a tarnished reputation or a lack of product consistency can turn-away customers and impact your product sales.
For example, let’s take apple juice -- the presence of the Alicyclobacillus bacteria can cause spoilage in the apple juice, ultimately affecting its taste. Picture a perfect sunny Sunday morning where you are sitting in your porch with your family and you open that apple juice and it turns out to be a smoky tasting apple juice – that’s why final membrane filtration is a crucial step in your production process, as it helps your juice retain its acidic taste and consistency while removing the unwanted particles.
With final membrane filtration to the rescue, you have nothing further to worry about, right?
Well… there’s one small caveat: How do you know that final filtration is actually doing its job?
The Need for Filter Integrity Testing
The goal of integrity testing is to ensure filter performance according the manufacturer claim. While there are a variety of filters available in the marketplace with fluctuating microbial retention characteristics based on multiple parameters such as challenge microorganisms used, challenge level and different performance claims are sometimes confusing resulting in filter performance misaddressing.
We can correlate the microorganism removal efficiency of the membrane filter performance using a specific challenge microorganism model which tends to prevent subsequent usages of the filter, referring to this test as is destructive. By comparison, a non-destructive test allows you to test the filter integrity and check for damage without compromising the filter future usage.
Manufacturers often perform destructive and non-destructive tests to validate the claims of their filter’s performance. But once these products exit a a manufacturer‘s shipping dock, they leave controlled environments. For example, a filter can sustain damage during shipment and installation that can go undetected without leveraging another round of integrity testing before use.
There are other opportunities when the filter can be compromised. When filters are cleaned and hot water sanitized or steamed for reuse, the change in conditions can cause stress to the filter hardware over time, eventually leaving them susceptible to damage .
To ensure that the filter maintains its integrity, Pall recommends that customers verify the integrity of the membrane filter before and after each batch is produced. This practice will enable isolating any potential compromised batches from ever leaving the factory floor .
How Pall Can Help
If you have never purchased a final membrane filter or integrity test device, you may not know which is best for your application. Our Pall SLS Global Technical Support team can help you achieve your process goals through process auditing and product recommendations based on application.
Protecting your brand is an everyday battle, but brand security is just a final membrane filter and integrity test device away -- both of which are the insurance policies for your business that you never knew you needed.
To learn how we can help you protect your food and beverage products, watch our webinar all about integrity testing, or contact your local Pall representative.
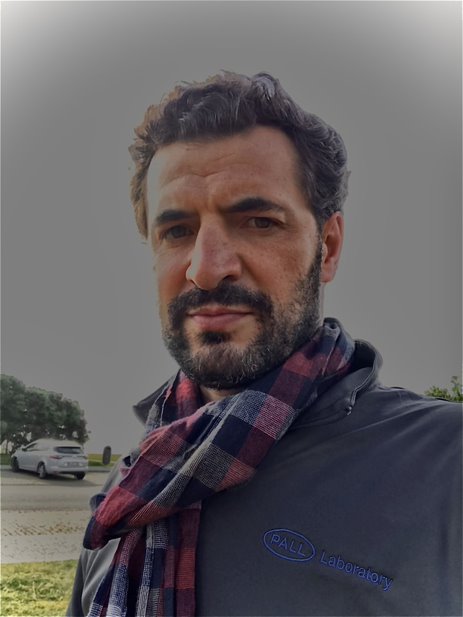
Bruno Pinto, SLS Global Technical Support Manager
- Category
- Author
- Sort By