27,000 megawatt lost turns into mega savings
Challenges
A 775 MW combined-cycle plant in the northeastern United States was experiencing premature plugging of resin pre-coated, backwashable condensate filter cartridges with resin fines and contaminants. This occurred especially during start-ups, when the contamination loading is at its highest. In addition to short runs, the plant also experienced filter bypass, end-cap failures, and system trips due to high filter differential pressure. The plant has a 275 MW steam turbine generator that uses an air-cooled condenser. The condensate polishing system consists of two Pall Septra™ backwash vessels in parallel, with one in operation and one on standby. Each vessel contains 420 filter cartridges, 2.50˝ diameter by 80˝ long.
The automated backwash cycle at the station consists of a sequence of operations that utilizes about 8,000 gallons of clean water, generating an equal amount of wastewater for each backwash event. The amount of resin and filter aid used for the pre-coat of the filters after each backwash is 100 cubic feet. The cost of the resin and the filter aid for each pre-coat is roughly $2,500 USD.
The plant had been using string-wound filter cartridges since its inception, but was experiencing several issues with performance and integrity. The biggest issue was short runs or low condensate throughput, especially during start-ups. The fouling of the string-wound filter media with particulate contaminant and the fine powder resin resulted in high differential pressure, resulting in by-pass of untreated condensate. In addition, there were instances of filter cartridge end-cap detachment, string “unwinding” due to repeated back flush and water hammer effects, and galling of the metal threads over time. Each such occurrence would require corrective action resulting in lost time and revenue.
Solution
The plant needed an experience team to help them eliminate contamination during start-ups. After careful consideration, Pall was chosen for the project. Pall Corporation has an international customer base, and a strong reputation for innovative solutions in the power and utilities industry. After attentively surveying the scene, Pall started to put its plan into action.
Considering the problems with the string-wound filters that the plant was experiencing, Pall recommended its Hydro-Guard® CoLD R condensate filter cartridges made with proprietary CoLD Melt™ technology. This technology creates a filtration matrix with small, micro-thin fibers for particle removal efficiency and Co-located Large Diameter (CoLD) fibers for the rigid structure and strength that is critical under the dynamic operating conditions encountered in this application. The filter cartridge offers reverse depth gradient pore structure that effectively captures particles on the finer porosity, tighter outer surface. At the inner depths of the filter exists a more open fiber matrix that facilitates a forceful and efficient backwash, which is critical to the performance and longevity of the filters.
The filter cartridges are made with 100% polypropylene, inert melt-blown fibers, containing no surfactants, wetting agents, or other extractables that are associated with string-wound construction, thus eliminating the issue of these materials contaminating the system. The absence of the extractable materials in melt-blown media saves time and water – both the clean water and the wastewater required to rinse off the extractable materials. A total of 420 Pall Hydro-Guard filter cartridges, 2.5˝ diameter by 80˝ long, were installed in the bottom tube-sheet vessel, without any modifications to the vessel.
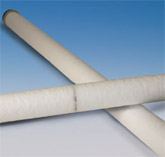
Hydro-Guard® CoLD R Series Filter Cartridges
Hydro-Guard CoLD R filter elements are manufactured using the CoLD Melt™ fiber production process. The CoLD Melt process permits the creation of multiple filtration zones within a single filter cartridge.
Results
Plant records show, five of the sixty-nine backwash cycles that the system underwent prior to the installation of the Pall cartridges were caused by high conductivity. Two were caused by resin trap problems. The rest were due to high differential pressure (DP). Since the installation of the Pall filter cartridges, the system has undergone 10 backwash cycles, all of which were due to water conductivity.
The power plant has reported an average throughput of 94.25 million gallons, which is about 4.4 times the throughput obtained with the string-wound filters between the backwash cycles. The longer runs have lessened the need for pre-coat resins, resulting in more than $60,000 in savings over a period of eight months. Based on the positive experience with the first vessel, the plant has retrofitted the second vessel. Since then, the plant has reported total cost savings of more than $140,000 over a period of 18 months. In the end, the installation of Pall’s Hydro-Guard Filters provided higher efficiencies, improved productivity and lower resin and chemical treatment costs.
Let’s find the right solution, together.
Let’s connect. We want to share our innovative filtration solutions with you today. Contact our knowledgeable subject matter experts for information on how we can help. Thank you and we look forward to assisting you shortly.