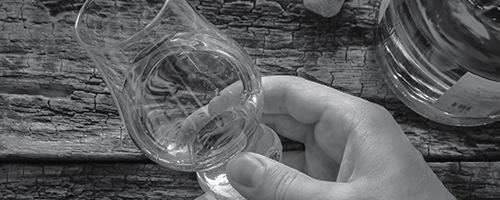
Blog
Three Ways a Non-Chill Filtration Whisky Process Will Save Your Distillery Money
June, 2023
It is the goal of spirit producers around the world to make stable, high-quality products that meet customer expectations and deliver good profitability. Filtration is one of the most challenging but crucial steps when producing spirits because of its impact on final product quality. Filter selection requires consideration of both its visual quality and its flavor characteristics. Undesirable turbid products can lead to customer complaints which could result in significant losses for the business from product recalls.
However, with spirits, the challenge is in the detail. Spirits are very fragile and sensitive liquids. Removing substances that may cause turbidity in the spirit based on the water and alcohol levels is essential. Whisky producers typically use a heat exchanger to remove chill haze. The purchase, maintenance and operation of the heat exchanger are the most expensive aspects of the distillation process.
Reducing the spirit temperatures to -2 °C and +4 °C (28.4oF and 39.2oF) before bottling creates precipitates of long-chain fatty esters, the cause of chill haze. In addition to causing chill haze, long-chain fatty esters can leave an unwanted taste, unlike short-chain fatty esters which give whiskey its taste and flavor. Selecting the appropriate filtration process that eliminates haze while preserving the most desirable aromas is a delicate balance. It is critical to remove only as much as necessary where haze is concerned so that the quality of the spirit is still intact.
Non-Chill Filtration Whisky Producer Example: How Did They Save Money?
For a famous leading whisky producer in Scotland, spirit quality is paramount. The producer repeatedly observed high filtrate turbidity which was out of specification for their process. High filtrate turbidity resulted in line downtime and a and a 0.5% reduction in line availability. After investigation, they found that their current chill filtration step they found that their current chill filtration step utilizing filter sheets was a majorroot cause of the existing out-of-spec turbidity.
Many producers are experimenting with chill haze removal using filtration without refrigeration which is known as “Non-Chill Filtration”. Based on Pall’s extensive reference installations in Scotland, the whisky producer was encouraged to consider Pall’s SUPRApak™ filtration technology as a possible solution. With support from Pall, the distiller successfully implemented a non-chill filtration process using SUPRApak SH modules.
As a demonstrated, three ways that non-chill filtration can help distilleries save money were identified:
- Increased distillery throughput & quality
By utilizing the non-chill process, they significantly reduced out-of-specification turbidity downtime. This resulted in increased distillery throughput and overall improvements in production. For example, the distiller experienced consistently lower bottling vat turbidity compared to the original chill filtration process using flat filter sheets.
- Reduced Production Costs
Production costs decreased throughout the entire non-chill process. This included reduced drip losses, improved availability of the filtration process, lower hold-up volume and less risk of product taint due to an improved blow out procedure.
- Energy Consumption Reduction
SUPRApak SH Modules eliminated the need for refrigeration. This provided economic gains for the producer thanks to reduced energy consumption.
To download the full bulletin, complete the form below and submit
- Category
- Author
- Sort By