Zum Schutz von Kompressoren, Brennerspitzen, Amin- und Glykoleinheiten, Molekularsieben und Quecksilberschutzbetten
Die Entfernung von Flüssigkeiten und Feststoffen aus einem Gasstrom ist bei Raffinations- und Gasverarbeitungsanwendungen sehr wichtig. Eine effektive Beseitigung dieser Verunreinigungen kann kostspielige Probleme und Ausfallzeiten von Downstream-Anlagen wie Kompressoren, Turbinen und Brennern verhindern. Zudem können Kohlenwasserstoffe und Feststoffverschmutzungen zu einer Schaumbildung in einem Amin-Kontaktorturm und zu vorzeitigen Wechseln von Katalysatoren in katalytischen Prozessen führen. In Kompressoren, die Öl zur Schmierung von Zylindern nutzen, gelangt das Schmieröl oft in das ausgelassene Gas, was zu einer Downstream-Kontamination führt. Ein dünner Film an Kohlenwasserstoffablagerungen an Wärmetauschern verdickt sich und sintert, wodurch die Wärmeübertragung verschlechtert, der Energieverbrauch erhöht wird und ein Risiko für Hot Spots und Undichtigkeiten entsteht.
Es sind mehrere Technologien zum Entfernen von Flüssigkeiten und Feststoffen aus Gasen verfügbar. Dieser Artikel erläutert zuerst die Auswahlkriterien für die folgenden Gas-flüssig-Separationstechnologien:
- Schwerkraftseparatoren
- Zentrifugenseparatoren
- Filterschaufelseparator
- Nebelabscheiderpads
- Flüssig-Gas-Koaleszer
und fokussiert sich anschließend auf die Separation feiner Aerosole mithilfe der Flüssig-Gas-Koaleszertechnologie.
Abscheidungsmechanismen
Vor der Evaluation spezifischer Technologien müssen wir die Mechanismen der Abscheidung von Flüssigkeiten und Feststoffen aus Gasen verstehen. Diese können in vier verschiedene Kategorien² unterteilt werden. Die erste und einfachste stellt die Absetzung durch Schwerkraft dar, die stattfindet, wenn das Gewicht der Tröpfchen oder Partikel (d. h. die Schwerkraft) den Luftwiderstand des fließenden Gases überschreitet.
Ein verwandter und effizienterer Mechanismus besteht in der Zentrifugenseparation; dieser Effekt greift, wenn die Zentrifugalkraft den Luftwiderstand des fließenden Gases überschreitet. Die Zentrifugalkraft kann erheblich stärker sein als die Schwerkraft.
Der dritte Separationsmechanismus wird als Trägheitsimpaktion bezeichnet. Dies findet statt, wenn Gas ein Netzwerk aus beispielsweise Fasern oder Impingement-Barrieren passiert. In diesem Fall folgt der Gasfluss einem gewundenen Pfad um diese Hindernisse herum; die Feststoffe oder flüssigen Tröpfchen tendieren zu einem geraden Weg und treffen auf die Hindernisse. Sobald dies geschieht, verlieren die Tröpfchen oder Partikel Geschwindigkeit und/oder koaleszieren und fallen schließlich auf den Boden des Behälters oder werden im Fasermedium zurückgehalten.
Ein vierter Separationsmechanismus findet schließlich bei sehr kleinen Aerosolen statt (unter 0,1 µm). Dieser Mechanismus, als diffusionale Interzeption oder Brownsche Bewegung bezeichnet, tritt auf, wenn kleine Aerosole mit Gasmolekülen kollidieren. Die Abweichung der Schwebstoffe vom Flussweg um die Barrieren herum aufgrund dieser Kollisionen erhöht die Wahrscheinlichkeit, dass Aerosole auf eine Faseroberfläche treffen und abgeschieden werden³.
Auf dieser Seite werden Tröpfchen- und Partikelgrößen in Mikrometer angegeben. Ein Mikrometer entspricht 1/1000 eines Millimeters oder 39/1.000.000 eines Zolls. Abbildung 1 zeigt die Größe verschiedener Materialien in Mikrometer.
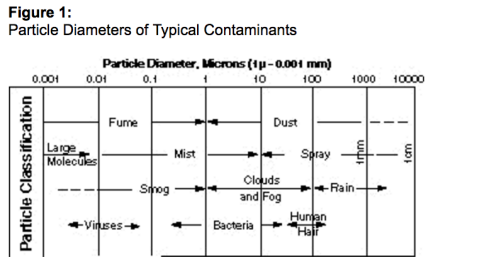
Abscheidungsmechanismen
Vor der Evaluation spezifischer Abscheidungstechnologien müssen wir die Mechanismen der Abscheidung von Flüssigkeiten und Feststoffen aus Gasen verstehen. Diese können in vier verschiedene Kategorien unterteilt werden.2 Die erste und einfachste stellt die Absetzung durch Schwerkraft dar, die stattfindet, wenn das Gewicht der Tröpfchen oder Partikel (d. h. die Schwerkraft) den Luftwiderstand des fließenden Gases überschreitet.
Ein verwandter und effizienterer Mechanismus besteht in der Zentrifugenseparation; dieser Effekt greift, wenn die Zentrifugalkraft den Luftwiderstand des fließenden Gases überschreitet. Die Zentrifugalkraft kann erheblich stärker sein als die Schwerkraft.
Der dritte Separationsmechanismus für Feststoffe und Flüssigkeiten aus Gasen wird als Trägheitsimpaktion bezeichnet. Dies findet statt, wenn Gas ein Netzwerk aus beispielsweise Fasern oder Impingement-Barrieren passiert. In diesem Fall folgt der Gasfluss einem gewundenen Pfad um diese Hindernisse herum; die Feststoffe oder flüssigen Tröpfchen tendieren zu einem geraden Weg und treffen auf die Hindernisse. Sobald dies geschieht, verlieren die Tröpfchen oder Partikel Geschwindigkeit und/oder koaleszieren und fallen schließlich auf den Boden des Behälters oder werden im Fasermedium zurückgehalten.
Ein vierter Mechanismus zur Separation von Flüssigkeiten/Feststoffen aus Gasen findet schließlich bei sehr kleinen Aerosolen statt (unter 0,1 µm). Dieser Mechanismus, als diffusionale Interzeption oder Brownsche Bewegung bezeichnet, tritt auf, wenn kleine Aerosole mit Gasmolekülen kollidieren. Die Abweichung der Schwebstoffe vom Flussweg um die Barrieren herum aufgrund dieser Kollisionen erhöht die Wahrscheinlichkeit, dass Aerosole auf eine Faseroberfläche treffen und abgeschieden werden.3
In dieser Abhandlung werden Tröpfchen- und Partikelgrößen in Mikrometer angegeben. Ein Mikrometer entspricht 1/1000 eines Millimeters oder 39/1.000.000 eines Zolls.
Abbildung 1 zeigt die Größe verschiedener Materialien in Mikrometer.

Flüssig-Gas-Separationstechnologien
Schwerkraftseparatoren
In einem Schwerkraftseparator oder Knock-Out-Abscheider wird die Separation mittels Schwerkraft vorgenommen. Je geringer die Gasgeschwindigkeit und je größer die Behältergröße, desto effizienter ist hier die Flüssig-Gas-Separation. Aufgrund der großen Behältergröße, die notwendig ist, um ein Absetzen zu erreichen, sind Schwerkraftseparatoren selten auf die Abscheidung von Tröpfchen einer Größe von unter 300 Mikrometer ausgelegt⁴. Ein Knock-Out-Abscheider wird normalerweise zur Bulk-Separation oder als erste-Stufe-Scrubber verwendet. Ein Knock-Out-Abscheider ist zudem nützlich, wenn die Innenteile im Behälter auf einem Minimum gehalten werden sollen, beispielsweise bei einem Entlastungssystem oder bei einem Betrieb, bei dem Fouling auftritt⁵. Wenn eine hohe Separationseffizienz erforderlich ist, werden Schwerkraftseparatoren nicht zum alleinigen Einsatz empfohlen.
Zentrifugenseparatoren
In Zentrifugen- oder Zyklonseparatoren können Zentrifugalkräfte mit einem Vielfachen der Schwerkraft auf ein Aerosol wirken. Im Allgemeinen werden Zyklonseparatoren verwendet, um Aerosole mit einem Durchmesser von über 100 µm abzuscheiden; ein Zyklon korrekter Größe kann zudem auch für Aerosole mit einer Größe von bis zu nur 10 µm eine akzeptable Abscheideeffizienz aufweisen. Die Abscheideeffizienz eines Zyklons ist bei Nebelpartikeln unter 10µm⁶ sehr niedrig. Sowohl Zyklone als auch Knock-Out-Abscheider werden für wachsartige oder verkokende Materialien empfohlen.
Nebelabscheider
Der Mechanismus der Nebelabscheider zur Separation von Feststoffen/Flüssigkeiten aus Gasen ist die Trägheitsimpaktion. Üblicherweise können Nebelabscheider aus Fasern oder gewirkten Sieben Tröpfchen mit einer Größe von 1–5 Mikron abscheiden; der Behälter dieser Abscheider ist jedoch verhältnismäßig groß, da die Geräte mit geringer Flussgeschwindigkeit betrieben werden müssen, um einen erneuten Einschluss von Flüssigkeiten zu verhindern.
Filterschaufelseparatoren
Schaufelseparatoren bestehen aus einer Reihe von Strömungsbrechern oder Platten in einem Behälter. Der Mechanismus der Separation ist ebenfalls die Trägheitsimpaktion. Die Abscheideeffizienz von Schaufelseparatoren ist gegenüber der Massengeschwindigkeit empfindlich; im Allgemeinen können Schaufelseparatoren jedoch mit höheren Geschwindigkeiten arbeiten als Nebelabscheider, der Hauptgrund hierfür liegt darin, dass eine effektivere Flüssigkeitsdrainage den Wiedereinschluss von Flüssigkeiten senkt. Aufgrund der verhältnismäßig großen Wege zwischen den Platten, aus denen das gewundene Netzwerk besteht, können Schaufelseparatoren jedoch nur verhältnismäßig große Tröpfchengrößen abscheiden (10 Mikrometer und größer). Oft werden Schaufelseparatoren verwendet, um Nebelabscheider-Behälter umzurüsten, wenn die Gasgeschwindigkeit die Auslegungsgeschwindigkeit überschreitet⁷.
Flüssig-Gas-Koaleszer
Flüssig/gas-Koaleszerelemente verbinden Merkmale von sowohl Nebelabscheidern als auch Schaufelseparatoren, sind aber üblicherweise nicht auf die Abscheidung von Bulkflüssigkeiten ausgelegt. In Bulkflüssigkeitssystemen wird üblicherweise ein hocheffizienter Koaleszer downstream eines Knock-Out-Abscheiders oder Impingement-Separators platziert. Das Gas fließt durch ein sehr feines Pack gebundener Fasermaterialien, deren Außenfläche umhüllt ist, um die Flüssigkeitsdrainage zu fördern (siehe Abbildung 2 unten). Ein Koaleszerelement kann Tröpfchen mit einer Größe von bis zu nur 0,1 Mikrometer zurückhalten. Bei korrektem Design und korrekter Größenbestimmung ermöglicht eine Drainage der koaleszierten Tröpfchen aus dem Faserpack erheblich höhere Gasgeschwindigkeiten im Vergleich zu Nebelabscheidern und Schaufelseparatoren, ohne dass es hierbei zu einem Wiedereinschluss von Flüssigkeiten oder einem höheren Druckabfall über die Baugruppe hinweg kommt.
Tabelle 1 fasst jede dieser Technologien zusammen und bietet Richtlinien zur korrekten Auswahl. Es ist ersichtlich, dass für Systeme mit sehr feinen Aerosolen unter 5 µm ein Koaleszer ausgewählt werden sollte. Die Abscheidung sehr feiner Aerosole aus Gasen resultiert in einem erheblichen Nutzen für Kompressorsysteme im Bereich Wirtschaftlichkeit, Zuverlässigkeit und Wartung.
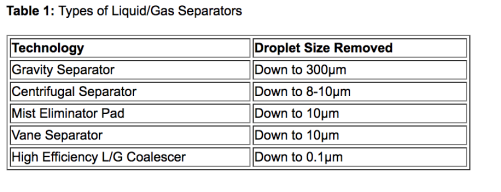
Bildung feiner Aerosole
Es gibt mehrere verschiedene Arten, auf die sehr feine flüssige Aerosole in einen Gasfluss eintreten können.
• Kondensation aus Sattdampf,
• Zerstäubung (Sprüheffekt durch eine Flussrestriktion) und,
• Erneuter Einschluss von Flüssigkeiten.8
Bei neueren Studien zur Aerosolgrößenverteilung in einem Erdgasfluss wurde festgestellt, dass Tröpfchen mit einer Größe unter 5 Mikrometer normal sind, wenn Drosselventile oder andere Hindernisse vorhanden⁹ sind oder Flüssigkeiten ihren Kondensationspunkt erreichen¹⁰. Die in Abbildung 3 gezeigten Messungen wurden durchgeführt, um die Konzentration flüssiger Aerosole in Erdgasflüssen zu bestimmen; die Proben wurden downstream der Schaufelseparatoren genommen (Kombination aus Schwerkraftseparatoren und horizontalen Filterbarrieren und äquivalenten Geräten mit einem Nebelabscheider). Die Ergebnisse zeigen, dass in vielen Fällen große Aerosolmengen diesen Typ Separator passieren können, da die Tröpfchen zu klein sind, um von diesen Separationsgeräten zurückgehalten zu werden. Daher sollte ein Flüssig-Gas-Koaleszer die erste Wahl darstellen, wenn hohe Wiederfindungsraten benötigt werden, um Downstream-Geräte zu schützen oder wertvolle Flüssigkeitsprodukte rückzugewinnen.

Filterfeinheiten/Größenbestimmung
Es muss beachtet werden, dass sich ein Koaleszer von einem Filter unterscheidet, da hier sowohl eine Filtration von festen Feinstpartikeln als auch eine Koaleszens flüssiger Aerosole aus einem Gasfluss vorgenommen werden. Die Größenbestimmung und die Feinheit eines Koaleszers sind bezüglich der Flüssigkeitsabscheidung von höchster Wichtigkeit für die letztendliche Leistung des Koaleszers. Ein zu kleiner Koaleszer führt zu einem kontinuierlichen Wiedereinschluss von Flüssigkeiten, einer sehr geringen Flüssigkeits-Gas-Separationseffizienz, und ist gegenüber Prozessänderungen sehr empfindlich. Die enorme Bedeutung der Koaleszer-Größenbestimmung ist in Abbildung 4 dargestellt; in dieser Abbildung wird gezeigt, dass die Koaleszerleistung rapide abfällt, sobald der Koaleszer zu viel Flüssigkeit verarbeiten muss (entweder aufgrund hoher Aerosolkonzentration im Gasfluss oder aufgrund hoher Gasflussrate). Dies stellt einen erheblichen Unterschied zu den meisten anderen Separationsgeräten dar, bei denen die Leistung bei Betrieb oberhalb der Auslegungswerte graduell abfällt.
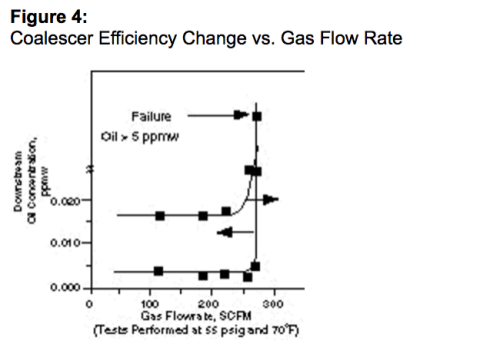
Eine herkömmliche Methode der Validierung der Koaleszerleistung ist der DOP-Test (Dioctylphthalat)¹¹. Bei diesem Test wird ein monodispergiertes Aerosol mit einem Durchmesser von 0,3 µm kontinuierlich durch Kondensation von DOP-Dampf unter kontrollierten Bedingungen erzeugt. Ist die Aerosol-Erzeugung stabilisiert (konstante Partikelgröße und Aerosol-Konzentration), wird die DOP-Konzentration upstream und downstream des Koaleszers mit einem Streulichtphotometer gemessen. Die Ergebnisse werden als Prozentsatz der DOP-Penetration bei der verwendeten Durchflussrate dargestellt.
Einige größere Nachteile des DOP-Tests umfassen¹²:
1. Der Test wird mit einem trockenen, ungesättigten Element durchgeführt. Ein trockenes Element verhält sich im Grunde genommen wie ein Schwamm und absorbiert jegliche passierende Flüssigkeit. Der DOP-Test misst nicht die Fähigkeit des Koaleszers zur Flüssigkeitsrückhaltung, wenn das Koaleszermedium mit Flüssigkeit gesättigt ist, die downstream wiedereingeschlossen werden könnten.
2. Dies führt zu einem zweiten Nachteil; der Druckabfall über das Gerät hinweg wird im Vergleich zum tatsächlichen Druckabfall über ein gesättigtes Element hinweg unterschätzt. Der gesättigte Druckabfall ist um das ungefähr 2–4-fache höher als der Druckabfall im Reinzustand.
3. Der Test wird unter partiellem Vakuum durchgeführt, unter dem sich die Gaseigenschaften (Dichte und Viskosität) erheblich von den Eigenschaften unter dem tatsächlichen Betriebsdruck unterscheiden. Unter DOP-Testbedingungen wird die Effizienz des Koaleszerelements tendenziell überschätzt.
Um die Unzulänglichkeiten des DOP-Test zu vermeiden, hat Pall den LASE-Test (Liquid Aerosol Separation Efficiency) entwickelt. Dieser Test wurde eigens für die Messung der Koaleszerleistung in einem Druckgasstrom unter Bedingungen, die den tatsächlichen Bedingungen in einer Raffinerie oder einem Gasaufbereitungswerk stärker ähneln, entwickelt. Das für diesen Test verwendete System ist schematisch in Abbildung 5 dargestellt.

Der LASE-Test unterscheidet sich wie folgt vom DOP-Test:
1. Er stellt eine präzisere und aussagekräftigere Effizienzmessung dar. Die DOP-Effizienz nennt im Grunde den Prozentsatz von 0,3 µm Dioctylphthalat-Tropfen, die von einem trockenen Koaleszer entfernt werden; der LASE-Test nennt den Anteil der Verunreinigungen in ppmw, die sich im Gas downstream des Koaleszers befinden. Anders gesagt nennt der LASE-Test die Menge an Verunreinigungen, denen Ihr Downstream-Equipment ausgesetzt wird.
2. Der DOP-Test verwendet monodispergierte (d. h. gleich große) Tropfen DOP, einer Flüssigkeit, die in Gasaufbereitungs- oder Raffinerie-Gasflüssen nicht oft vorgefunden wird; der LASE-Test verwendet ein Schmieröl mit Tropfengrößen von 0,1–0,9- µm.
3. Der LASE-Test bildet die Prozessbedingungen genauer nach, da er mit einem gesättigten Element unter positivem Druck durchgeführt wird.
Tabelle 2 zeigt einen Vergleich zwischen DOP- und LASE-Test.

Die Auswirkung des Designs auf die Größenbestimmung
Das Ziel bei der Verbesserungen des Koaleszerdesign ist die Effizienzmaximierung bei gleichzeitiger Verhinderung eines Wiedereinschlusses von Flüssigkeiten. Ein Wiedereinschluss tritt auf, wenn auf einem Koaleszerelement gesammelte Flüssigkeitstropfen von ausströmendem Gas abgetragen werden. Dies geschieht, wenn die Geschwindigkeit des ausströmenden Gases, die Ringraumgeschwindigkeit, die Schwerkraft des ablaufenden Tropfens übersteigt.
Die Wichtigkeit einer korrekten Koaleszer-Größenbestimmung wurde bereits erwähnt. Bei Design und Größenbestimmung eines Koaleszers müssen die folgenden Parameter beachtet werden:
- Gasgeschwindigkeit durch das Medium,
- Ringraumgeschwindigkeit von aus dem Medium austretenden Gas,
- Konzentrationen von festen und flüssigen Aerosolen im Einlassgas und
- Entleerfähigkeit des Koaleszers
Jeder dieser Faktoren mit Ausnahme der Aerosol-Einlasskonzentration kann gesteuert werden. Bei einem konstanten Gasfluss kann die Mediengeschwindigkeit gesteuert werden, indem entweder die Grobheit der Porenstruktur des Mediums verändert oder die Anzahl der verwendeten Elemente erhöht oder verringert wird. Je gröber das Medium, desto geringer ist jedoch die Effizienz des Koaleszers bei der Flüssigkeitsabscheidung.
Bei einem konstanten Gasfluss kann die Auslassgeschwindigkeit des Gases gesteuert werden, indem die Größe des Behälters oder des Raums zwischen den Elementen erhöht oder verringert wird.
Die Drainage kann entweder durch Auswahl von Koaleszermaterialien mit geringer Oberflächenenergie oder durch Behandlung des Koaleszermediums mit einer Chemikalie, die die Oberflächenenergie des Mediums auf einen Wert unterhalb der Oberflächenspannung der zu koaleszierenden Flüssigkeit senkt, verbessert werden¹³. Ein Material mit geringer Oberflächenenergie verhindert ein Benetzen des Filtermediums mit Flüssigkeit und beschleunigt die Drainage von Flüssigkeiten entlang der Medienfasern herab. Die auf dem Fasermaterial koaleszierte Flüssigkeit fällt schnell durch das Fasernetzwerk, ohne sich in den Poren anzusammeln; dort würde es ansonsten durch das Gas durch die Poren gedrückt und wieder mitgeführt werden. Abbildung 6 zeigt den Effekt, den eine chemische Behandlung auf den Koaleszer haben kann. Hier ist gezeigt, dass die maximale Durchflussrate eines chemisch behandelten Koaleszers bei mehr als dem Doppelten eines ähnlichen, unbehandelten Elements liegt.
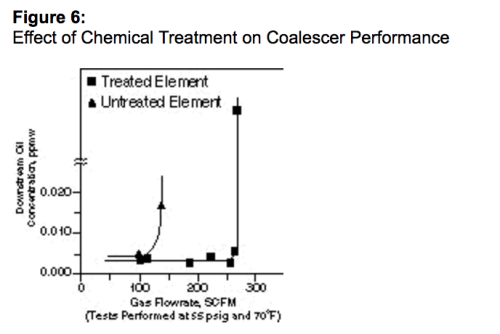
Aus diesen Designparametern lässt sich schließen, dass ein großes Gehäuse mit einer großen Anzahl Elemente mit sehr feinen Poren jedes Flüssigkeitsproblem in einem Gasstrom einfach lösen könnte. Die Kosten eines solchen Behälters wären natürlich sehr hoch. Durch Reduzierung der Behältergröße und Elementanzahl steigt die Wahrscheinlichkeit eines Wiedereinschlusses und einer schlechteren Abscheideeffizienz. Zudem wächst mit sinkender Gerätegröße der Druckabfall, was zu höheren Betriebskosten führen kann. Daher ist eine Optimierung erforderlich. Bei der Evaluierung eines Koaleszers müssen bei der Größenbestimmung alle diese Parameter miteinbezogen werden. Ein Koaleszer wird im Idealfall in Kombination mit einem Knock-Out-Abscheider oder anderen Impingement-Separatoren verwendet.
Feldversuche für Flüssig-Gas-Koaleszer
Durch Feldversuche an einem Gasfluss, aus dem Flüssigkeiten entfernt werden müssen, können folgende Informationen gewonnen werden:
1. die Flüssigkeitsmenge im Gas,
2. Die Fähigkeit, Flüssigkeiten effizient zu koaleszieren, und
3. Die Menge an vorhandenen festen Feinstpartikeln.
Dementsprechend ist eine präzise Probenahme von höchster Bedeutung. Es ist sehr wichtig, die Gasflussraten durch ein Test-Koaleszerelement präzise zu messen, um die Menge und Eigenschaften der im Gas vorhandenen Flüssigkeit bestimmen zu können.
Für diesen Zweck wurde ein vollständiges Testkit konstruiert, um Seitenstrom-Flüssig-Gas-Koaleszerprüfungen durchzuführen. Dieses Testkit ist in Abbildung 7 dargestellt. Es enthält: (1) Ein Koaleszergehäuse für ein Element, über einen kleinen Kugelhahn mit einem unabhängigen Sammelbehälter verbunden; (2) einen Öffnungs-Flussmesser downstream des Koaleszergehäuses einschließlich Flanschen, Öffnungsplatte und Differenzdruckmanometer; (3) ein Nadelventil zur Regelung des Gasflusses durch das Koaleszergehäuse; (4) zwei Probenahmeanschlüsse upstream und downstream des Koaleszergehäuses, an die zwei der Gas-Testkits simultan angeschlossen werden können, um Zufluss- und Abflussgasqualität zu analysieren; und (5) zwei lange, flexible Edelstahlschläuche, die das Testkit mit der Hauptgasleitung und der Abgasleitung verbinden.

Testverfahren
Vor der Durchführung eines Feldversuchs vor Ort werden die Systembedingungen des Werkes erfragt (Druck, Temperatur, Gasflussrate, Typ des Gases und falls möglich, Flüssigkeitskonzentration im Gasfluss). Basierend auf diesen Informationen wird eine Öffnungsplatte zur Messung der Gasflussraten im relevanten Bereich ausgewählt. Die Öffnung wird ebenfalls so ausgewählt, dass der Druckabfall minimiert wird, sodass keine Gaskondensation und Hydratbildung ausgelöst wird.
Nachdem das Seitenstrom-Testkit online ist, wird die Durchflussrate unterhalb der kritischen Durchflussrate eingestellt, so dass es zu keinen erneuten Einschlüssen kommt. Ist das Koaleszerelement gesättigt, werden Testmembranen in Prüf-Haltevorrichtungen upstream und downstream des Koaleszergehäuses eingesetzt; der Sammelbehälter wird von allen Flüssigkeiten entleert, die sich möglicherweise während der Sättigung des Elements angesammelt haben, und der eigentliche Test beginnt.
Nach Ende des Tests wird das Volumen der im Sammelbehälter gesammelten Flüssigkeit gemessen; die Flüssigkeit wird in einem Probenröhrchen für weitere Analyse im Labor entnommen. Zudem werden ebenfalls die Testmembranen entnommen, um die Menge an Schwebstoffen im Gas zu untersuchen und eine qualitative Identifizierung der festen Verunreinigungen vorzunehmen. Die Konzentration flüssiger Aerosole wird aufgrund der Menge koaleszierter Flüssigkeit und der Menge an getestetem Gas bestimmt.
Ergebnisse des Feldversuchs
Die Ergebnisse von Feldversuchen an 49 Gasflüssen (Erdgas, Kohlendioxid, Wasserstoff und Brenngas) sowohl in Gasaufbereitungsanlagen als auch Raffinerien zeigen, dass in den meisten Gasflüssen erhebliche Flüssigkeitsmengen vorliegen. In Abbildung 8 sind diese Testergebnisse zusammengefasst. Von den 49 geprüften Strömen wiesen 85 % (43 von 49 Tests) Flüssigkeitskonzentrationen von über 1 ppmw auf. Diese Flüssigkeitskonzentration kann zu erheblichen Problemen in rotierenden Geräten führen und zu schlechtem Prozessbetrieb in einem aminberührenden Gerät beitragen.
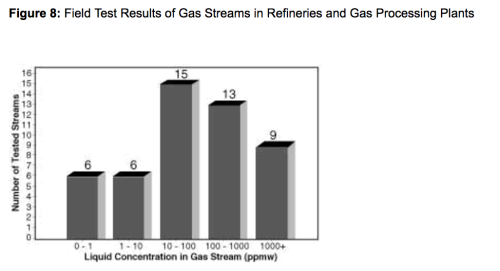
Schlussfolgerungen
1. Die Auswahl von Gas-Flüssig-Separationstechnologien erfordert nicht nur Kenntnisse der Prozessbedingungen, sondern zudem Wissen über die Eigenschaften der flüssigen Verunreinigungen. Die Auswahl sollte basierend auf Tröpfchengröße, Konzentration und eventuell vorliegenden Wachs- oder Foulingtendenzen der Flüssigkeit vorgenommen werden.
2. Durch eine Analyse von Praxisdaten wurde gezeigt, dass aufgrund des Vorhandenseins sehr feiner Flüssigkeitstropfen (unter 1 Mikron) in den meisten Gasprozessen hocheffiziente Flüssig-Gas-Koaleszer empfehlenswert sind, wenn hohe Wiederfindungsraten zum Schutz von Downstream-Geräten oder zur Rückgewinnung wertvoller Flüssigkeiten erforderlich sind.
3. Größenbestimmung und Design des Koaleszers sind von höchster Wichtigkeit. Muss ein Koaleszer zu viel Flüssigkeit verarbeiten, entweder aufgrund von übermäßigen Aerosolkonzentrationen oder einer hohen Gasflussrate, sinkt die Effizienz rapide ab.
4. Der LASE-Test (Liquid Aerosol Separation Efficiency) ist ein aussagekräftiger Leistungstest von Flüssig-Gas-Koaleszern, da hier die Koaleszerelemente unter Bedingungen geprüft werden, die den tatsächlichen Betriebsbedingungen sehr nahe kommen (gesättigtes Element, realistischer Druckabfall und Gaseigenschaften (Dichte, Viskosität)).
5. Eine Oberflächenbehandlung des Koaleszermediums verbesserte die Flüssigkeitsdrainage der Fasermaterialien und verringerte die zur Verarbeitung eines bestimmten Flusses erforderliche Elementanzahl um 50 %.
6. In Feldversuchen wurde gezeigt, dass erhebliche Flüssigkeitsmengen im Gasstrom von Raffinerien und Gasaufbereitungswerken vorhanden sind.
Referenzen
1. C.R. Pauley, D.G. Langston, and F. C. Betts, “Redesigned Filters Solve Foaming, Amine Loss Problems at Louisiana Gas Plant,” Oil & Gas Journal, Feb. 4.1991.
2. Perry’s Chemical Engineers’ Handbook, 6. Edition, McGraw-Hill, New York, 1984, Chap. 18, pp.48–56.
3. Perry’s Chemical Engineers’ Handbook, 6. Edition, McGraw-Hill, New York, 1984, Chap. 18, pp.48–56.
4. K. J. Fewel Jr., J. A. Kean, “Computer Modeling Aids Separator Retrofit, ”Oil & Gas Journal, 6. Juli 1992.
5. A. K. Coker, “Computer Program Enhances Guidelines for Gas-Liquid Separation Designs”, Oil & Gas Journal, 10. Mai 1993.
6. Perry’s Chemical Engineers’ Handbook, 6. Edition, McGraw-Hill, New York, 1984, Chap. 18, pp.48–56.
7. K. J. Fewel Jr., J. A. Kean, “Computer Modeling Aids Separator Retrofit,” Oil & Gas Journal, 6. Juli 1992.
8. Perry’s Chemical Engineers’ Handbook, 6. Edition, McGraw-Hill, New York, 1984, Chap. 18, pp.48–56.
9. C. A. G. Regan und M. Baker, “A Novel Separator/Scrubber Design Program - The Impact of Upstream and Downstream Equipment on Separation Performance,” auf dem 9. Continental Meeting of the Gas Processing Association, European Chapter, vorgestellte Arbeit, Mai 14–15, 1992.
10. Perry’s Chemical Engineers’ Handbook, 6. Edition, McGraw-Hill, New York, 1984, Chap. 18, pp.48–56.
11. C. Dickenson, “Filters and Filtration Handbook,” 3. Edition, Elsevier Adv. Tech, Oxford, 1992, pp. 44–47.
12. K. Williamson, S. Tousi und R. Hashemi, “Recent Developments in Performance Rating of Gas/Liquid Coalescer,” auf dem 1. Annual Meeting of the American Filtration Society vorgestellte Arbeit, März 21–25, Ocean City, MD.
13. J. D. Miller, E. E. Koslow, K. W. Williamson, U. S. Patent 4.676.807, Jun. 30, 1987; id., U. S. Patent 4.759.782, Jul. 26, 1988.
Unsere Produkte
Branchenführende Produktlösungen, die die Anforderungen Ihrer Kunden erfüllen.